Purpose Of Wing Slots
This slot machine gets you coming and going. Win River Casino / Aristocrat - - - - - Key: Most videos are 'Double, Bonus or Goose' (DBG). There are two main types of flaps. Trailing edge Flaps and Leading edge flaps. Slats are used to improve the low speed characteristics of the airplane. Deploying them changes the shape of the wings which gives it a better lift producing capability. In some aircraft, the slats are fixed, which opens up a slot between the wing and the slat. In this case, the terms slot and slat are used interchangeably. 'Leading edge slot' by Sanchom - Own work. Licensed under CC BY 3.0 via Commons. A number of airliners use movable slats, in which case, the system is called slat, rather than slot. The point at which the air flow gets divided into two paths is known as the stagnation point. As angle of attack of an aircraft is increased, its stagnation point moves toward the bottom of the wing. And energy of the air flowing over the top of the wing reduces. And hence the air flow separates from the top of the wing.
secondary flight controls
In addition to primary flight controls, most airplanes have another group called secondary controls. These include trim devices of various types and wing flaps. The trim devices are adjusted so that the aircraft remains balanced in flight.
Flaps
Flaps are moveable surfaces on the trailing edge of the wing similar in shape to the ailerons. they are usually larger in surface area. They are located on inboard end if the wing next to the fuselage. Both sides are activated together so they do not produce a rolling action like the ailerons.Flaps are usually deployed in 'degree' increments. In small aircraft deployment is usually in 10 degree increments from zero degrees (non-deployed) to 40 degrees maximum. Larger or more sophisticated aircraft may have a different range of settings. Normally, the flaps operate electrically through a 4 or 5 position switch located on the instrument panel. In earlier aircraft the flaps were operated using a manual flap handle.
Deployment of flaps increases both the lift and drag of the wing. Flap activation increases the angle of attack across the wing / flap section. At 10 degrees, more lift than drag is produced. As the flap angle is increased more drag and less lift is produced for each increment of deployment.

The primary use of flaps is in landing. They permit a steeper decent without increase in airspeed. Flaps may be used in certain take-off situations (usually 10°) on short or soft fields.
Flaps are now fitted to most aircraft because:
They permit a slower landing speed, which decreases the required landing distance.
They permit a comparatively steep angle of descent without an increase in speed. This makes it possible to safely clear obstacles when making a landing approach to a small field.
They may also be used to shorten the takeoff distance and provide a steeper climb path.
VFE
This term describes the maximum velocity at which flaps can be deployed. The VFE is shown on the air speed indicator as the top end of the white arc.
Flaps are high lift devices which, in effect, increase the camber of the wing and, in some cases, as with the Fowler Flap, also increase the effective wing area. Their use gives better take-off performance and permits steeper approach angles and lower approach and landing speeds.

When deflected, flaps increase the upper camber of the wing, increasing the negative pressure on the top of the wing. At the same time, they allow a build up of pressure below the wing. During take-off, flap settings of 10 degrees to 20 degrees are used to give better take-off performance and a better angle of climb, especially valuable when climbing out over obstacles.
However, not all airplane manufacturers recommend the use of flaps during take-off. They can be used only on those airplanes, which have sufficient take-off power to overcome the extra drag that extended flaps produce. The recommendations of the manufacturer should, therefore, always be followed.
Flaps do indeed increase drag. The greater the flap deflection. the greater the drag. At a point of about half of their full travel, the increased drag surpasses the increased lift and the flaps become air brakes. Most flaps can be extended to 40 degrees from the chord of the wing. At settings between 20 degrees and 40 degrees, the essential function of the flaps is to improve the landing capabilities, by steepening the glide without increasing the glide speed. In an approach over obstacles, the use of flaps permits the pilot to touch down much nearer the threshold of the runway. Flaps also permit a slower landing speed and act as air brakes when the airplane is rolling to a stop after landing, thus reducing the need for excessive braking action. As a result, there is less wear on the undercarriage, wheels and tires. Lower landing speeds also reduce the possibility of ground looping during the landing roll.
Plain and split flaps increase the lift of a wing, but at the same time, they greatly increase the drag. For all practical purposes, they are of value only in approach and landing. They should not normally be employed for take-off because the extra drag reduces acceleration.
Slotted flaps, on the other hand, including such types as Fowler and Zap, produce lift in excess of drag and their partial use is therefore recommended for take-off.
From the standpoint of aerodynamic efficiency, the Fowler Flap is generally considered to offer the most advantages and the fewest disadvantages, especially on larger airplanes, while double slotted flaps have won wide approval for smaller types.
On STOL airplanes, a combination of double slotted flaps and leading edge slats are common.
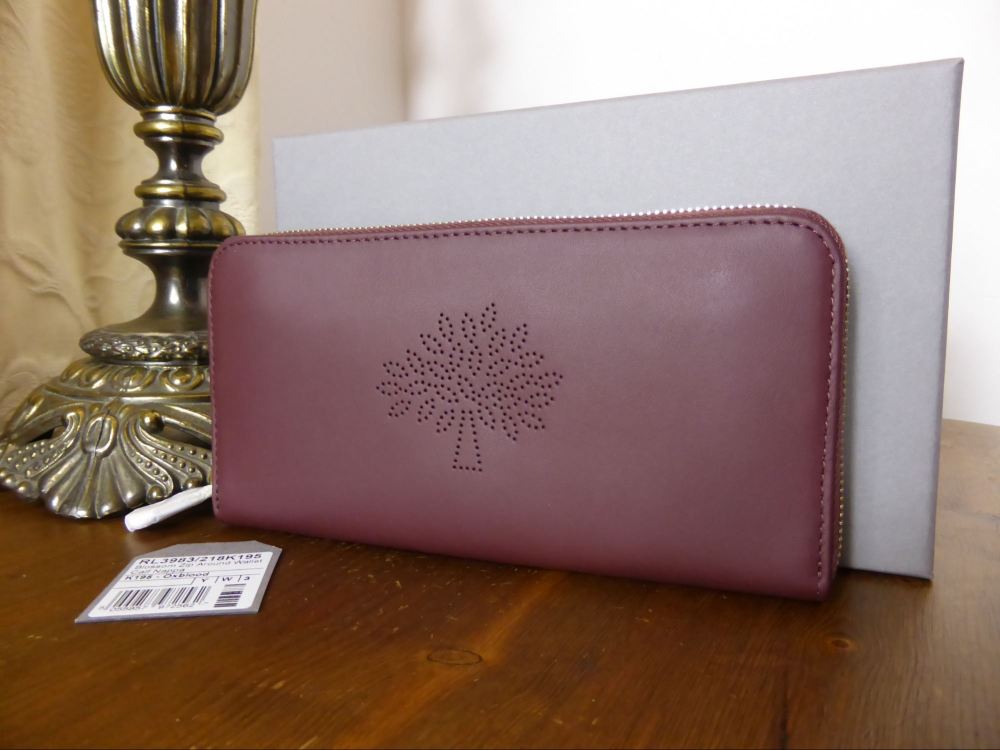
Changes in flap setting affect the trim of an airplane. As flaps are lowered, the centre of pressure moves rearward creating a nose down, pitching moment. However, in some airplanes, the change in airflow over the tailplane as flaps are lowered, is such that the total moment created is nose up and it becomes necessary to trim the airplane 'nose down'.
The airplane is apt to lose considerable height when the flaps are raised. At low altitudes, therefore, the flaps should be raised cautiously.
Most airplanes are placarded to show a maximum speed above which the flaps must not be lowered. The flaps are not designed to withstand the loads imposed by high speeds. Structural failure may result from severe strain if the flaps are selected 'down' at higher than the specified speed.
When the flaps have been lowered for a landing, they should not ordinarily be raised until the airplane is on the ground. If a landing has been missed, the flaps should not be raised until the power has been applied and the airplane has regained normal climbing speed. It is then advisable to raise the flaps in stages.
How much flap should be used in landing? Generally speaking, an airplane should be landed as slowly as is consistent with safety. This usually calls for the use of full flaps. The use of flaps affects the wing airfoil in two ways. Both lift and drag are increased. The Increased lift results in a lower stalling speed and permits a lower touchdown speed. The increased drag permits a steeper approach angle without increasing airspeed. The extra drag of full flaps results in a shorter landing roll.
An airplane that lands at 50 knots with full flaps selected may have a landing speed as fast as 70 knots with flaps up. If a swerve occurs during the landing roll, the centrifugal force unleashed at 70 knots is twice what it would be at 50 knots, since centrifugal force increases as the square of the speed. It follows then, that a slower landing speed reduces the potential for loss of control during the landing roll. It also means less strain on the tires, brakes and landing gear and reduces fatigue on the airframe structure.
There are, of course, factors, which at times call for variance from the procedure of using full flaps on landing. These factors would include the airplane's all-up-weight, the position of the C.G., the approach path to landing, the desired rate of descent and any unfavourable wind conditions, such as a strong cross wind component, gusty winds and extreme turbulence. With experience, a
pilot learns to assess these various factors as a guide to flap selection.
In some airplanes, in a crosswind condition, the use of full flap may be inadvisable. Flaps present a greater surface for the wind to act upon when the airplane is rolling on the ground. The wing on the side from which the wind is blowing will tend to rise. In addition, cross wind acting on full flaps increases the weather vaning tendencies, although in an airplane with very effective rudder control even at slow speeds, the problem is not so severe. However, in many airplanes, the selection of full flaps deflects the airflow from passing over the empennage, making the elevator and rudder surfaces ineffective. Positive control of the airplane on the ground is greatly hampered. Since maintaining control of the airplane throughout the landing roll is of utmost importance, it may be advisable to use less flaps in cross wind conditions. In any case, it is very important to maintain the crosswind correction throughout the landing roll.
trim tabsA trim tab is a small, adjustable hinged surface on the trailing edge of the aileron, rudder, or elevator control surfaces. Trim tabs are labour saving devices that enable the pilot to release manual pressure on the primary controls.
Some airplanes have trim tabs on all three control surfaces that are adjustable from the cockpit; others have them only on the elevator and rudder; and some have them only on the elevator. Some trim tabs are the ground-adjustable type only.
The tab is moved in the direction opposite that of the primary control surface, to relieve pressure on the control wheel or rudder control. For example, consider the situation in which we wish to adjust the elevator trim for level flight. ('Level flight' is the attitude of the airplane that will maintain a constant altitude.) Assume that back pressure is required on the control wheel to maintain level flight and that we wish to adjust the elevator trim tab to relieve this pressure. Since we are holding back pressure, the elevator will be in the 'up' position. The trim tab must then be adjusted downward so that the airflow striking the tab will hold the elevators in the desired position. Conversely, if forward pressure is being held, the elevators will be in the down position, so the tab must be moved upward to relieve this pressure. In this example, we are talking about the tab itself and not the cockpit control.
Rudder and aileron trim tabs operate on the same principle as the elevator trim tab to relieve pressure on the rudder pedals and sideward pressure on the control wheel, respectively.
The tabs are usually controlled by a wheel which is often situated on the floor between the two front seats. Some aircraft have the trim controlled by a small rocker switch on the control column. The aircraft should be trimmed after every change in attitude or power setting. It takes a little practice to trim an aircraft, but in the end it is done unconsciously.
other wing additions
The type of operation for which an airplane is intended has a very important bearing on the selection of the shape and design of the wing for that airplane. Wing fences, slots, slats, spoilers, speed brakes and flaps are additions to the wing that perform a variety of functions related to control of the boundary layer, increase of the planform area (thus affecting lift and drag) and reduction of aircraft velocity during landing and stopping.
wing fences
Wing fences are fin-like vertical surfaces attached to the upper surface of the wing, that are used to control the airflow. On swept wing airplanes, they are located about two-thirds of the way out towards the wing tip and prevent the drifting of air toward the tip of the wing at high angles of attack. On straight wing airplanes, they control the airflow in the flap area. In both cases, they give better slow speed handling and stall characteristics.
slots
Slats are auxiliary airfoils fitted to the leading edge of the wing. At high angles of attack, they automatically move out ahead of the wing. The angle of attack of the slat being less than that of the mainplane, there is a smooth airflow over the slat which tends to smooth out the eddies forming over the wing. Slats are usually fitted to the leading edge near the wing tips to improve lateral control. The Socata Rallye is an example of a light aircraft that utilizes leading edge slats.
Slots are passageways built into the wing a short distance from the leading edge in such a way that, at high angles of attack, the air flows through the slot and over the wing, tending to smooth out the turbulence due to eddies.
Purpose Of Wing Slots Game
spoilers
Purpose Of Wing Slots Poker
spoiler on an F4 Phantom wing
Spoilers are devices fitted to the wing which increase drag and decrease lift. They usually consist of a long narrow strip of metal arranged spanwise along the top surface of the airfoil. In some airplanes, they are linked to the ailerons and work in unison with the ailerons for lateral control. As such, they open on the side of the upgoing aileron, spoil the lift on that wing and help drive the wing down and help the airplane to roll into a turn.

In some airplanes, spoilers have replaced ailerons as a means of roll control. The spoiler moves only upward in contrast to the aileron that moves upward to decrease lift and downward to increase lift. The spoiler moves only up, spoiling the wing lift. By using spoilers for roll control, full span flaps can be used to increase low speed lift.
Spoilers can also be connected to the brake controls and. when so fitted, work symmetrically across the airplane for producing drag and destroying lift after landing, thereby transferring all the weight of the airplane to the wheels and making braking action more effective.
speed brakes
RF-84K Thunderflash speed brake
Speed brakes are a feature on some high performance airplanes. They are a device designed to facilitate optimum descent without decreasing power enough to shock cool the engine and are especially advantageous in airplanes with high service ceilings. They are also of use in setting up the right approach speed and descent pattern in the landing configuration. The brakes, when extended, create drag without altering the curvature of the wing and are usually fitted far enough back along the chord so as not to disrupt too much lift and in a position laterally where they will not disturb the airflow over the tailplane. They are usually small metal blades housed in a fitting concealed in the wing that, when activated from the cockpit, pivot up to form a plate. On some types of aircraft, speed brakes are incorporated into the rear fuselage and consist of two hinged doors that open into the slipstream.
Ever wondered why F1 designers go to such extraordinary lengths to refine the design of the front wings and particularly the endplates? Top teams bring something new in this area to almost every race.
When you look down into this area of the car's design, you realize that it has far more effect on the aerodynamics than the much discussed double diffuser - probably five to ten times more effect! The front wing, unlike the rear, does not just provide downforce. As it is the aerodynamic device that precedes the entire car, it is also responsible for directing airflow back towards the rest of the car. The optimal direction of this airflow is of critical importance to the overall downforce levels produced by the entire car.
Double Diffusers grab all the headlines, largely because of the legality issues arised 2009, but they are nothing like as important to an F1 car as the barely discussed 'outwash' front wing.
Outwash front wing after 2009 rule change | Inwash front wing after 1998 rule change |
The front wings on the car can produce 25-40% of the cars downforce. Each front wing is made of mainplane running almost the whole width of the car suspended from the nose. Onto this are fitted two aerofoil flaps, one on each side, which are from 2009 the adjustable parts of the wing. These flaps are usually made of one piece of carbon fiber, but Ferrari has used two small flaps rather than one large one. On each end of the mainplane there are endplates.
The wing flaps on either side of the nose cone are asymmetrical. They reduces in height nearer to the nose cone as this allows air to flow into the radiators and to the underfloor. If the wing flap maintained it's height right to the nose cone, the radiators would receive less airflow and therefore the engine temperature would rise. The asymmetrical shape also allows a better airflow to the underfloor and the diffuser, increasing downforce. The wing mainplane is by the FIA rules flat in the center and same design for all cars, again by the rules. This again allows a slightly better airflow to the underfloor aerodynamics, but it also reduces the wings ride height sensitivity. The main area of development is the wing profile interaction with the front wing endplate.
So, now I'm going to give the outwash wing, the spotlight it deserves.
One very important part of the front wing is the endplate design. The endplate is used to redirect the airflow around the front tyres; the tyres are certainly not designed to be aerodynamically efficient and can create a lot of drag. By directing the oncoming airflow around the front tyres, this minimises the amount of drag resistance produced and allows the airflow to continue back to the sidepods and the cars floor. The upper and main flap also helps direct airflow over the front tyres, reducing drag as well as producing airflow towards the rest of the car.
The front wing tip vortex and the front wheel wake are the most important things to control in F1 aerodynamics. You want to stop vortexes and the front wheel wake to go in places where they do too much damage. 50-60% of the aerodynamics of front wing is concentrated on this vital area.
In 1998 when F1 cars were with new rules narrowed in width from 2 metres to 1.8 metres the cars ended up with the front wing endplate alongside the inside edge of the front tire. Designers developed very sophisticated solutions to manage the front wheel wake and wing tip vortex in order to get lots of downforce.
But then in 2009 the FIA brought in a radical change of aerodynamic rules, one of which was to make the front wing wider. Now, with the tips of the front wing sitting directly ahead of the front wheels, it was a completely different story.
The more experienced engineers in the pit lane, who had been around before 1997, or who had worked on IndyCars or Le Mans cars, knew that it would be desirable to produce an outwash effect from the front wing endplate, which would generate a low pressure area on the outside of the front wheel. It would also avoid the front flap being blocked by having a wheel right behind it.
Front wing endplate on 2010 Renault R30 f1 racer on presentation of new car at beginning of 2010 season.
Over time, as the wheels were moved closer to the chassis, the front wings ends overlapped the front wheels when viewed from the front. This created unnecessary turbulence in front of the wheels, further reducing aerodynamic efficiency and thus contributing to unwanted drag.
To overcome this problem, the top teams made the inside edges of the front wing endplates curved to direct the air far from the casis and around the wheels. The primary function of endplate is to stop the high-pressure air on the top of the wing from being encouraged to roll over the end of the wing to the low-pressure air beneath, causing induced drag. Additionally, the design aim of the endplates is to discourage the 'dirty' air created by the front tire from getting under the floor of the car. Further to these, some teams use 'splitters', which are vertical fences, attached to the undersurface of the front wing, to assist the endplate

Front wing endplate on BMW-Sauber 2009 racer |
Toyota were one of the first to try it, thanks to the intervention of veteran aerodynamicist Frank Dernie, and it was one of the signature items on the Brawn car who win 2009 championship. Engineers say that the outwash front wing was the single biggest step from 2008 to 2009, far more than the double diffuser.
Brown BGP001 racer with highly sophisticated end plate for 2009 season
McLaren 2009 outwash wing endplate
Year 2010, every car in the pit lane has one, with varying degrees of sophistication.
Red Bull has a very pronounced vortex channel underneath the end of the wing. If you look really closely there are lots of new details, sometimes tiny, sometimes very pronounced every race weekend, because the front wing, and particularly the tip of it, is an incredibly sensitive area and the tiniest change to a turning vane can make a big difference to the car's performance.
Ferrari made a good gain in Melbourne 2010 with the new wing endplate detail you can see in picture. Ferrari endplate is relatively simple but very effective. this is the proof that simple wing can be good wing.
Some of the 2010 new teams like Lotus (picture left and above) HRT and Virgin have fairly crude front wings and refining them will bring a big step forward in performance, moving them closer to the midfield teams. Lotus show few important updates during the season 2010. On the end, they finished 2010 championship on 10th place, the best of new teams.
For Virgin Racing, whose designer Nick Wirth insists on using only CFD (computational fluid dynamics) in the design and development of his car, this will be a real test and the whole pit lane is watching to see how well he does it.
This is because the main weakness of CFD in F1 design is in the area of modeling front wheel wake. It is so complex and changes with every tiny movement in the attitude of the car and movement of the steering wheel.
Rival engineers, who also have big CFD capability in their factories, say it's not possible to accurately measure front wheel wake using F1 standard CFD alone. This is because the air flow in the wheel wake is unsteady and the only CFD program capable of modeling unsteady flow is owned by NASA and costs $1 million a month to run!
If the rivals are right then this will hold Virgin racing back. But if Wirth comes up with a major step in this area, then the others may begin to concede that he has found an affordable way to do away with wind tunnels.
Renault showed modest pace in 2010 pre-season testing and in first race in Bahrain, but took a step forward in Australia, thanks partly to a new front wing (pictured left).
They introduced a sophisticated new outwash front wing solution and it contributed a significant amount to the car's improvement. You can see the difference from the wing endplate introduced on presentation of new car at beginning of 2010 season, picture you can see on the beginning of this article.
And in China they have come along with a further front wing update.
Compare this with the photo above. A lot of work has gone into the curvature of the upper front element and particularly into the detailing of the end plates. The new ones feature (1) a shorter and less vertical fin than the Melbourne wing and (2) a squarer end to the upper element.
These changes have primarily the effect of reducing the turbulence generated in this area of the car, and also reduce the front end's sensitivity to variations in the ride heights.
During season 2010, Renault brought many new parts to their car, especially front wings, from a revamped aerodynamics department. They claimed that the fully evolved R30 (race at Abu Dhabi), which did so much damage to Fernando Alonso’s championship hopes, was two seconds per lap faster than the version which raced in Bahrain at the start of the season.
That gain is made up of the F-Duct and blown diffuser, both worth roughly 4/10ths of a second per lap, depending on circuit, plus “ten front wing packages, five floors, two engine covers, six rear wing packages, seven front brake drum and cooling duct packages, and three rear brake drum and brake cooling duct packages,” according to the team.
But now Renault have gone even further with the concept. In recent races the team have produced a new take on the flap design. The version raced since Germany 2011 has split one of the flaps into two. This along with the slot in the main plane creates a stack of five elements for a small span of the front wings width. But in contrast to other uses of extra slots in the front wing, this is not to create a section producing high downforce. Instead each of these steps is designed to create tip vortices to drive airflow along the axis 250mm from centerline (so called axis Y250).
Teams tend to create the greater amount of downforce towards the front outer wing tips. This pressure distribution reduces the load on the inboard end of the wing, in order to better manage the airflow headed below the car. However what teams do want to do is to use the relatively undisturbed airflow along this axis and use it to drive airflow over the centre of the car. A steeper wing towards the neutral 50cm centre section of wing would produce unwanted turbulence and rob the airflow of energy. The bodywork rules do allow for some creativity with the vanes and other bodywork allowed along the edge of the monocoque. Known as the Y250 vortex, as most of the aerodynamic effects are created along a line starting 25cm from the cars centreline (Y= lateral axes, 250mm). Components that work along this axis include the front wing mounting pillars, any under-nose vanes, the T-Tray splitter and the intersection of the front wing and the neutral centre section. Flow structures along this axis drive airflow under the floor towards the diffuser and around the sidepod undercuts. Each with the aim to create more efficient rear downforce.
If Renault created a single front wing element with the same angle of attack, a single large vortex would have been produced. This would be far more powerful and pointed outwards a smaller area downstream on the car. By splitting the wing into smaller separate sections, several smaller vortices are created. These are each of lower energy and are spread over wider area. Use of vortices are to shape and alter flow over other areas of the car. Vortices are extremely high energy structures. Vortices travel down the sides of the car and act as a barrier. If this vortex generators are positioned correctly, these vortices keep high-pressure air around the car from entering the low-pressure underbody region, thus maintaining more downforce. Perhaps this softer Renault approach creates less sensitivity as the cars attitude changes.
Some more pictures of 2010 cars front wing endplate:
Force India
Mercedes GP F1 racer
McLaren endplate in the middle of season 2011, artwork
McLaren endplate in the middle of season 2012, artwork
As we can see, front wing development is not primarily about adding front downforce, but about cleaning up flow to the rest of the car and crucially, adding stability when the front wheels are turning through a corner. These tiny details on the front wing are working for that and it seems to be working good.